2015 Joint Mathematics Meetings
Jeannye Dudley
Artists
Jeannye Dudley
Project Architect
Stanley Beaman Sears
Atlanta, Georgia
Statement
My passion is geometry, art and architecture. With each project I search for ways explore creativity and complexity. Over the past year I investigated computational designs using 3d parametric software GRASSHOPPER from Rhino v5. Once the geometry was in the computer, it became necessary to learn about mesh geometry for rendering with the software, Luxology and VRay for Rhino. I am fascinated by the new medium of 3D printing and how this methodology may inform architecture design and fabrication. The design parameters are shifting towards an accurate transfer of digital data from the tool maker to the product builder. Product fabrication pricing structure may be driven by material density and volume making COMPLEXITY ESSENTIALLY FREE.
Artworks
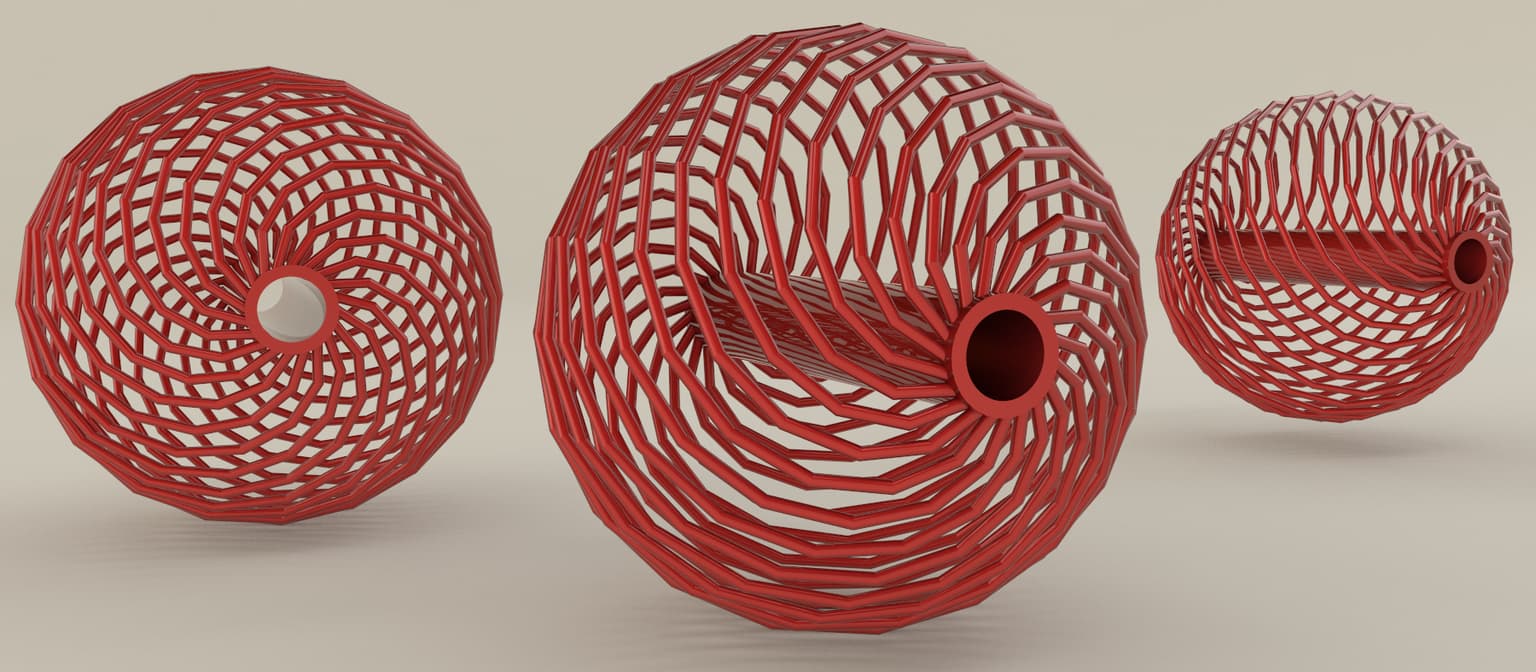
Half Diagrid on Sphere
5" in diameter
Model in Rhino and Grasshopper Rendering in VRay
2014